What is Green Steel?
- Sustainable practices: Incorporating scrap steel recycling into production to lower the carbon footprint – Induction Furnace (IF) + Electric Arc Furnace (EAF)
- Low-Carbon Steel Production – Renewable Power + Direct Reduction of Iron (DRI) + EAF
- Carbon Neutral Steel – ‘Net-Zero’ emissions, either by eliminating emissions entirely or by offsetting residual emissions through carbon capture, utilization, and storage (CCUS)
- Green Hydrogen-based steelmaking: Replacing coke or coal with hydrogen to reduce iron ore
Conventional Steel Making
Currently as per global statistics, 71% of steel is currently made using the BF-BOF process, with 29% produced by the EAF method. (Source: World Steel Association -WSA)
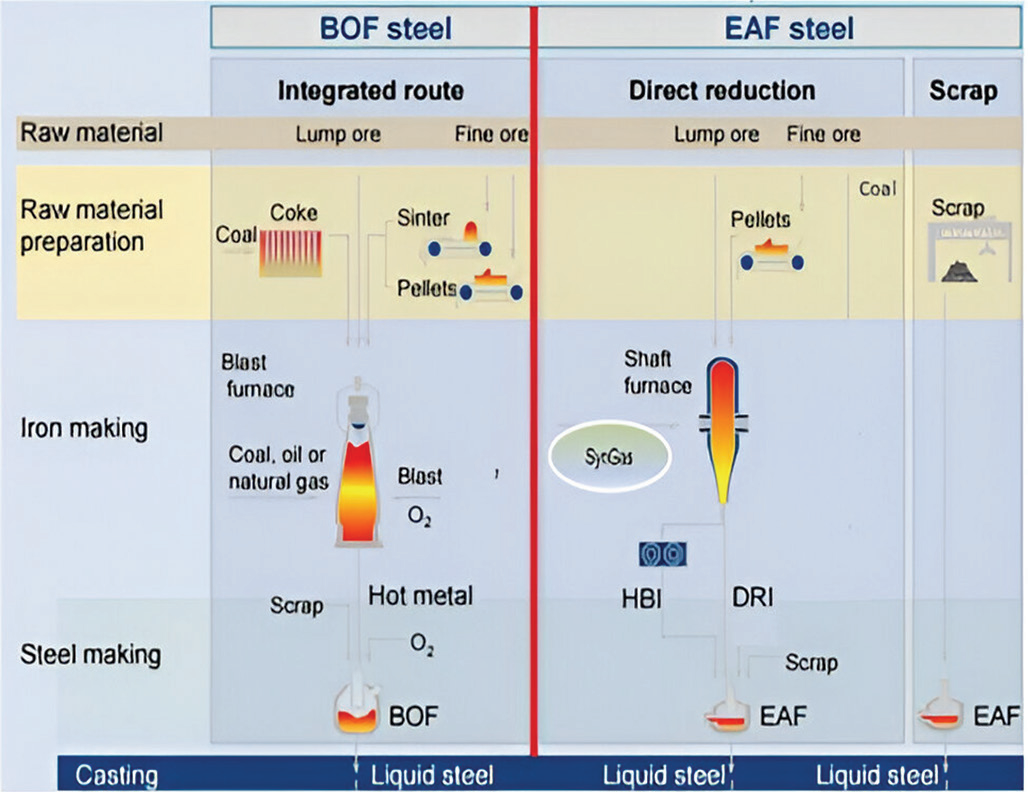
Present
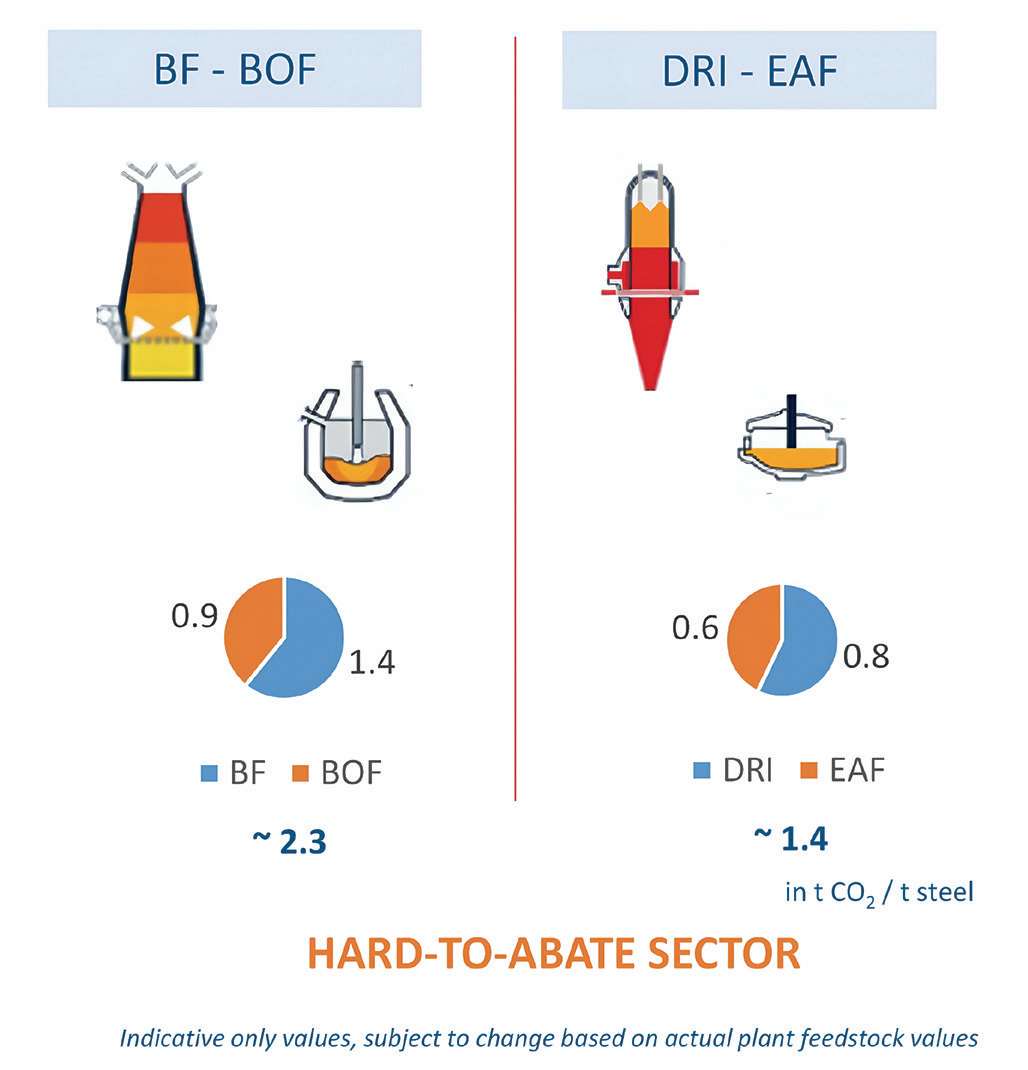
Dev Energy already has delivered end-to-end turnkey solution offering in scrap processing with Induction Furnace (IF) + Electric Arc Furnace (EAF) over a decade delivering 0.6 – 0.7 t CO2/t Steel
Basics of Low-Carbon Steel Making
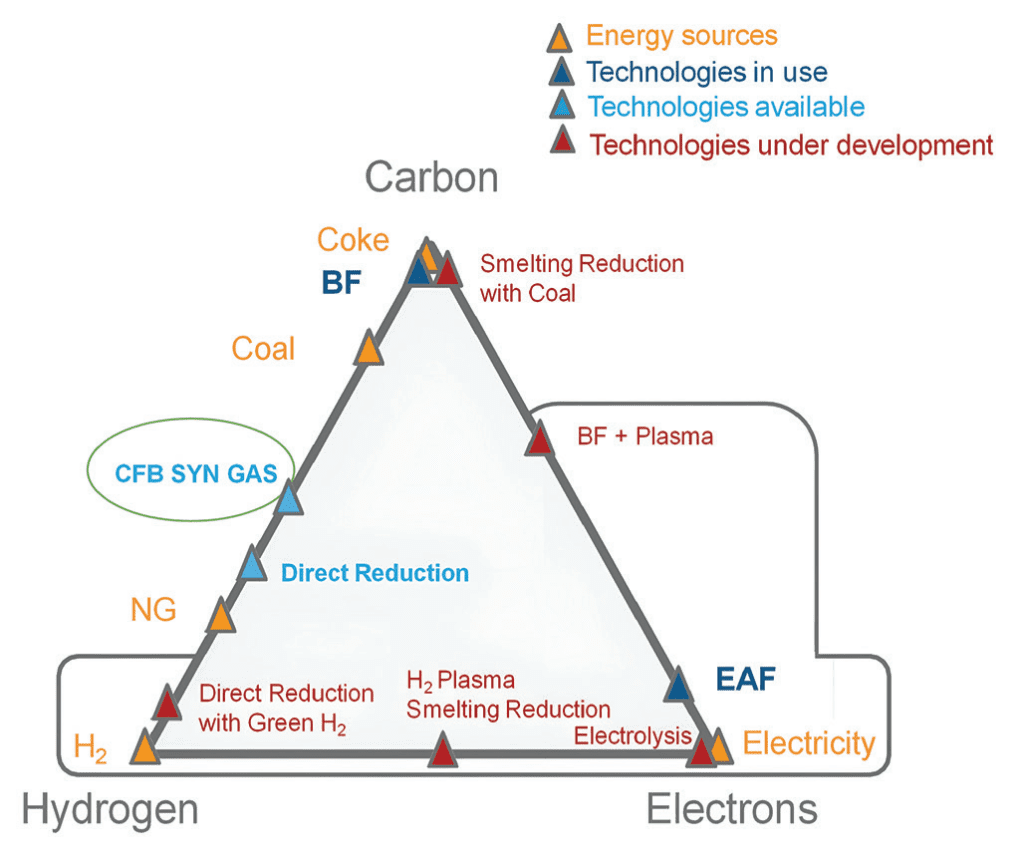
Technology Selection – Why CFB?
Commercial scale three technologies which are Fixed Bed, Entrained Flow and Fluidised Bed technologies below pros and cons:
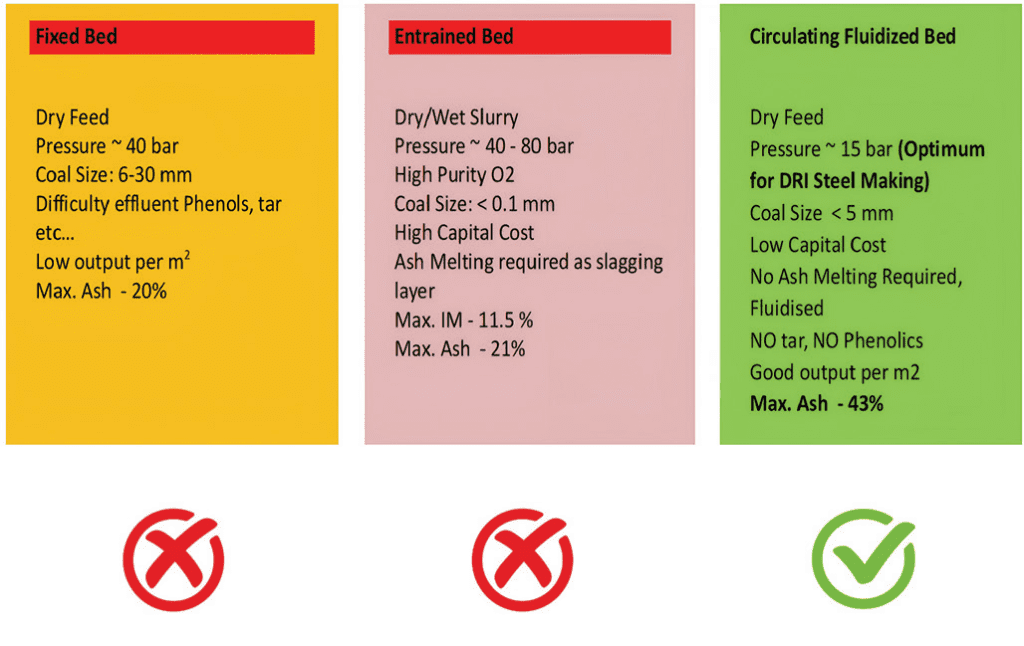
Based on various interactions organised by the Ministry of Coal for the implementation of the National Coal Gasification mission it is evident that all major technology developers such as Thermax, BHEL and CSIR-CIMFR have chosen CFB starting with pilot scale as the most suitable technology for Indian high ash coal.
Future - Sustainability
CFB gasification as detailed below is flexible coal gasification technology with advantage of handling high ash (as applicable to India scenario) and when combined with already matured technologies, water shift and CO2, H2S removal units can deliver flexible DRI SYN Gas composition at optimised pressure and temperature in overall high efficiency economical solution as compared to conventional Natural Gas reforming.
CFB Technology Overview
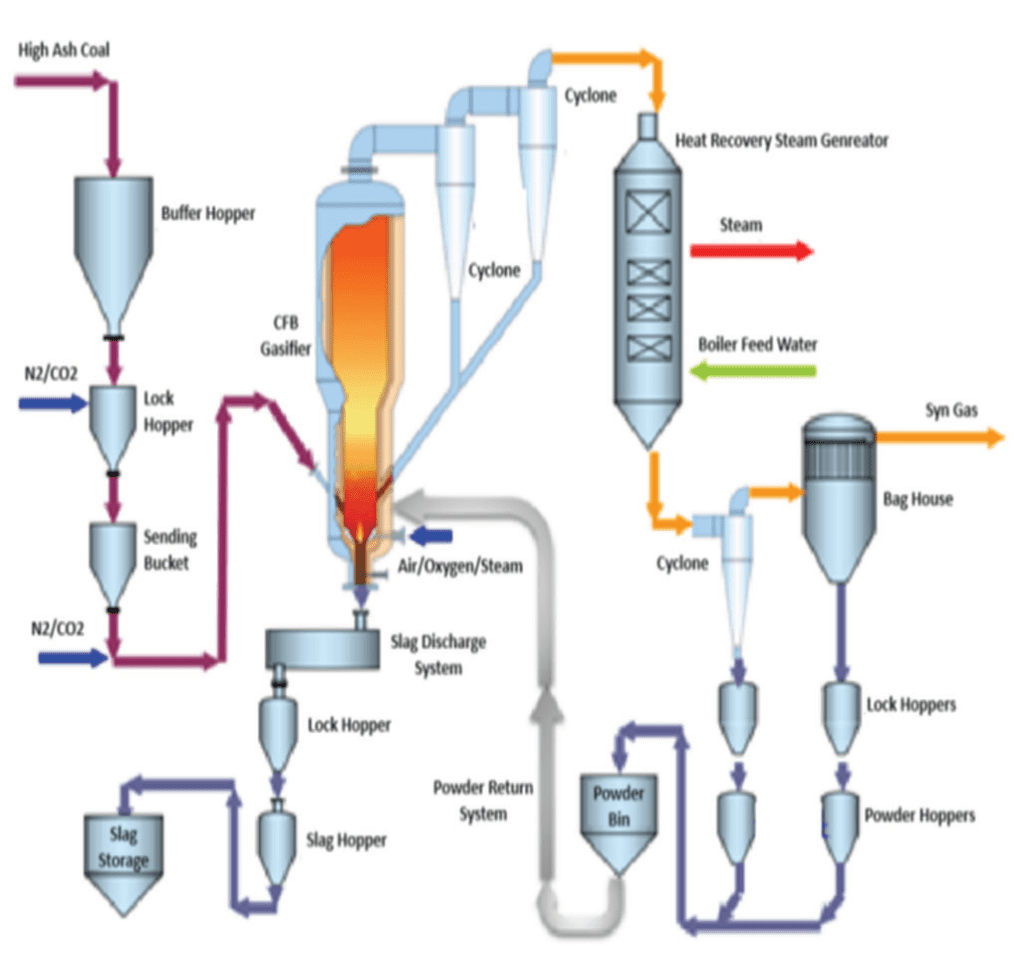
CFB Technology – How It Works?
Circulating Fluidized Bed (CFB) technology is a coal gasification process where solid fuels are converted into a syn gas (majorly H2, CO, CH4) at high temperature in presence of gasification agents oxygen/air and steam.
Grinding, sorting, shredding, and/or drying may be required to bring the feedstock up to the gasifier feed system’s standards of <10 mm particulate size.
The prepared feedstock is pneumatically supplied to the CFB gasifier vessel, which is a bubbling in circulating fluidized bed reactor. The feedstock combines with air/oxygen and steam as gasification in the fluidized bed, uniform temperature of 1000 C is maintained to provide high carbon conversion and non-slagging conditions for the feedstock’s ash.
The CFB gasification process is carried out as partial oxidations as gasification of feedstock with agglomeration and separation of ash.
Ash is removed by gravity from the gasifier and is discharged into a system for depressurization and disposal. The gasifier maintains a low level of carbon in the bottom ash discharge stream and achieves overall carbon conversions that can exceed 96%.
CFB is more fuel-flexible, utilizing low-rank and other high- ash coals, and offers higher efficiency than competing gasification technologies, due to the fluidized bed design and resulting long residence times of the reacting particles.
Fines carried over from the fluidized bed are separated from the syngas prior to heat recovery and syngas cleanup. The product syngas is essentially free of tars and oils due to the temperature and residence time of the gases in the fluidized bed, simplifying downstream heat recovery and gas cleaning operations.
CFB gasification adopts three-stage waste heat recovery process, which can recover the heat of high temperature syngas to produce high temperature and high pressure steam along with air/oxygen preheating resulting in overall high thermal efficiency
CFB Technology Features & Advantages
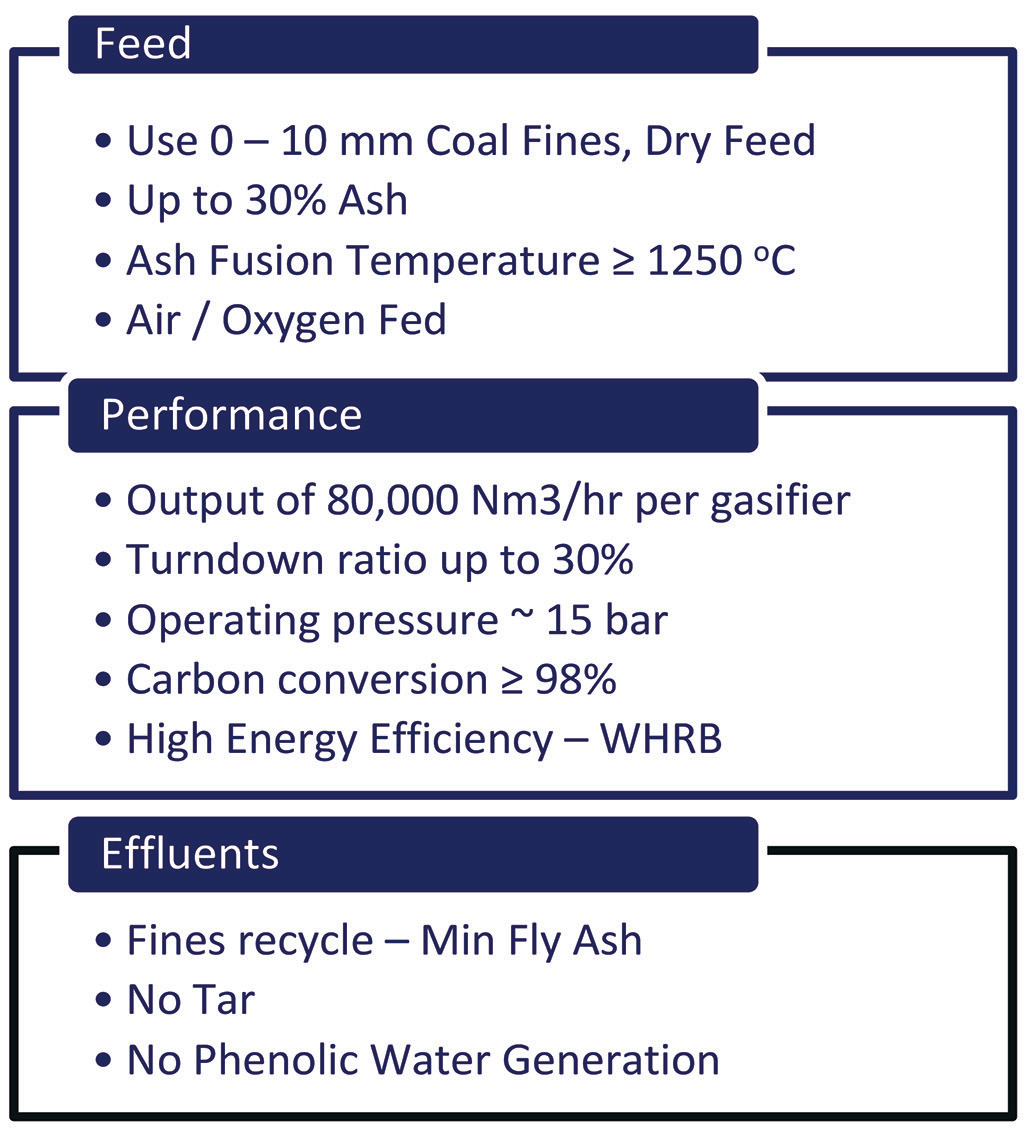
Our Partners
JINAN HUANGTAI GAS FURANCE CO. LTD.
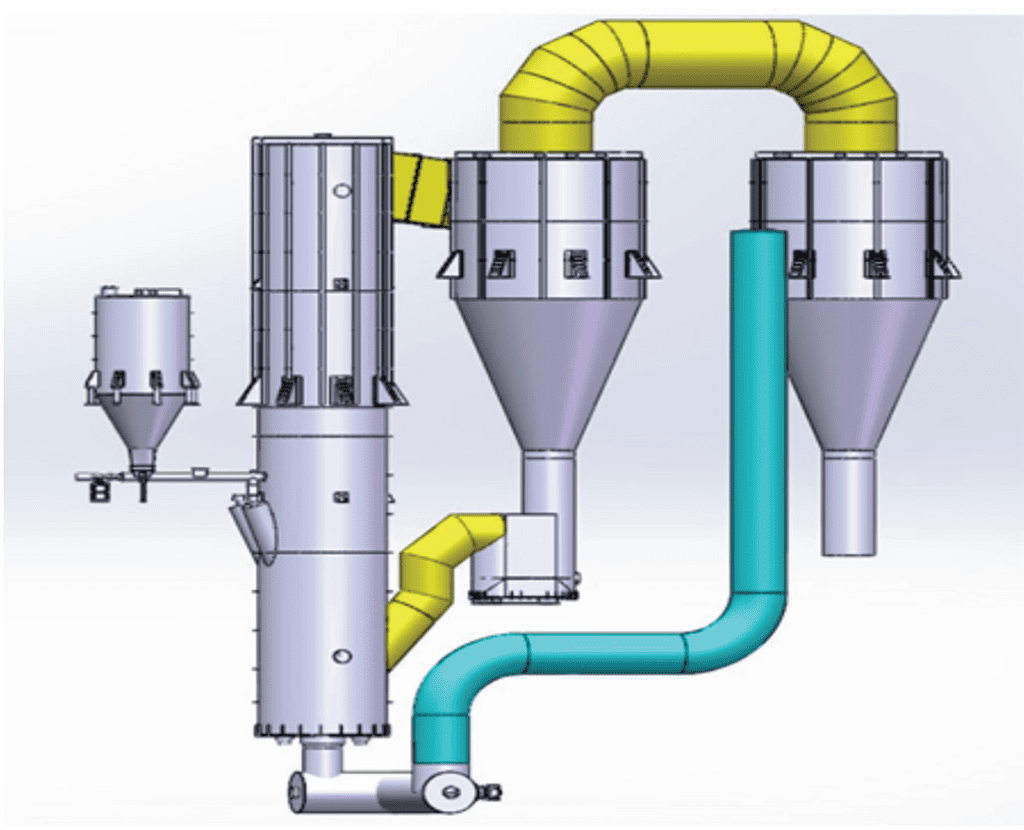
Normal Pressure – Air Fed - Fuel
– In Operation Since 2009
– > 22 Operational plants
– Higher calorific value fuel : 1250 kcal/Nm3
– Continuous 21 month gasifier campaign
– Ease of Operation & Maintenance
SHANGHAI ZEPU ENGINEERING TECHNOLOGY CO. LTD.
Normal Pressure – Air Fed - Fuel
– Patented and improvised CFB technology
– High Pressure – 3 bar to 40 bar
– Proven commercial scale plants from basic engineering, detailed engineering, and EPC solutions for clean SYN GAS
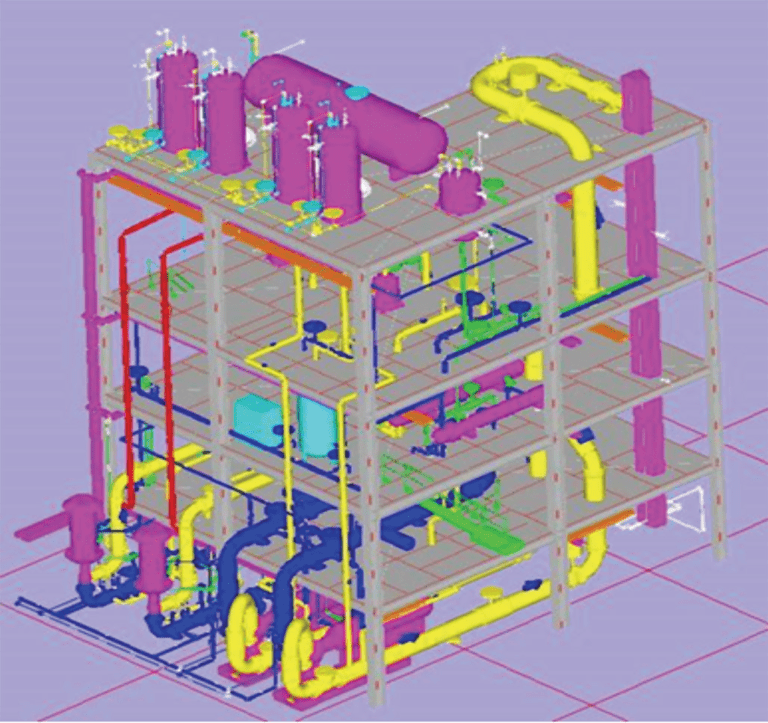
Optimized Process Configuration
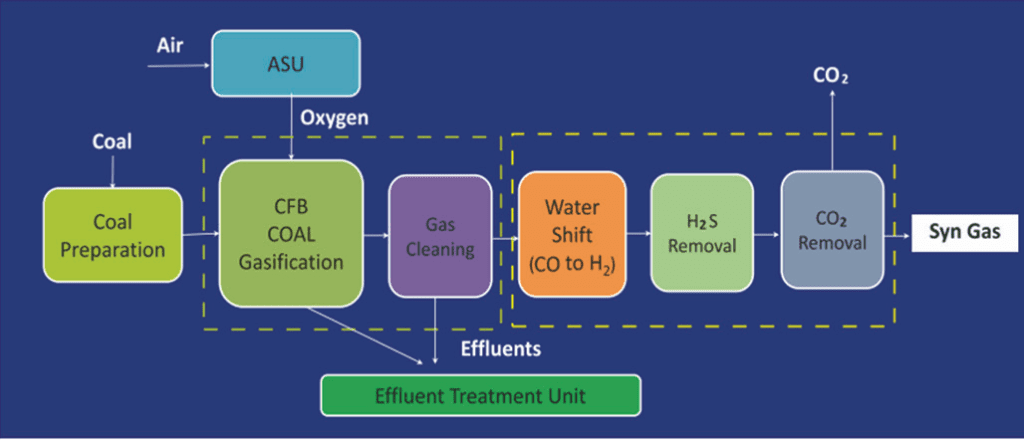
Compatibility with Downstream DRI Licensors
CFB technology with complete package as DRI SYN GAS solution has full flexibility of H2/CO ratio such as 1.1, 1.6 or even future -proof 100% Blue H2 with CCUS.
Dev Energy offers as required by all global vertical shaft DRI technology Liensors making it wide adaptability for overall technical and commercial optimisation to make Green Steel.
Commercial DRI Plant – Ready for Offering
0.5 MTPA DRI – Vertical Shaft Kiln
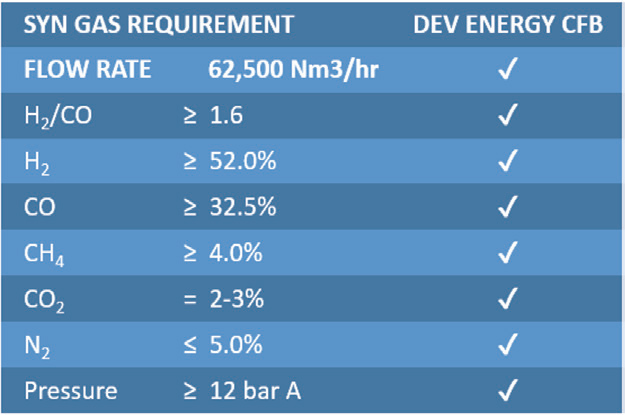
Flexibility of CFB Offering
CFB gasification adopts oxygen-enriched gasification, and the N2 content in syngas can be effectively controlled below 5% or lower. CFB gasification pressure is high avoiding any downstream compression requirement, and the CH4 content in the syngas can be up to Controlled ideal for DRI steel-making feedstock.
Advantages
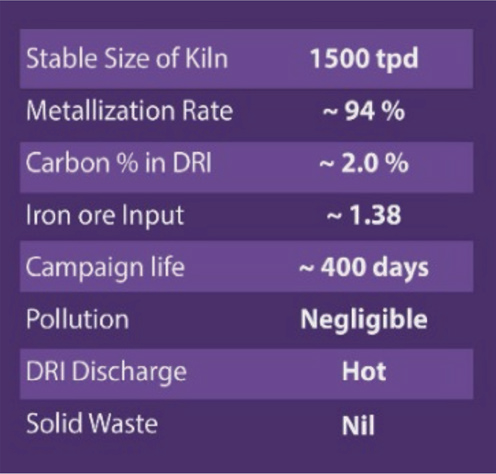
Green Steel Path Forward
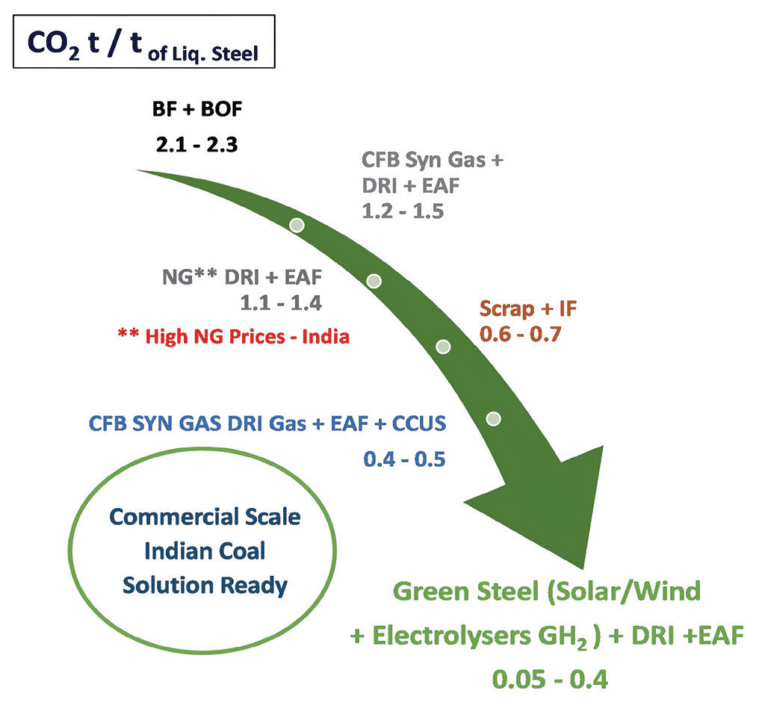
Conclusion
DEV ENERGY with its successful Turnkey project design and implementation proven solution provider has delivered > 23 years and is committed to Sustainable Green Steel Solution with exclusive partnerships already in place. With experienced & qualified EPC solution provider not only can coal gasification projects for DRI SYN GAS as path forward for Green Steel on fast track but also provide after sales service and operational success.