Importance Of Secondary Steel Sector
Secondary steel provides a convincing answer for sustainable practices. Recycling and rerolling methods not only reduce environmental impact they also ensures high-quality goods that fulfil industrial requirements. As the construction industry prioritizes sustainability, using secondary steel is critical for a greener future. That is where secondary Steel Melting Shop (SMS) becomes critical to achieve this.
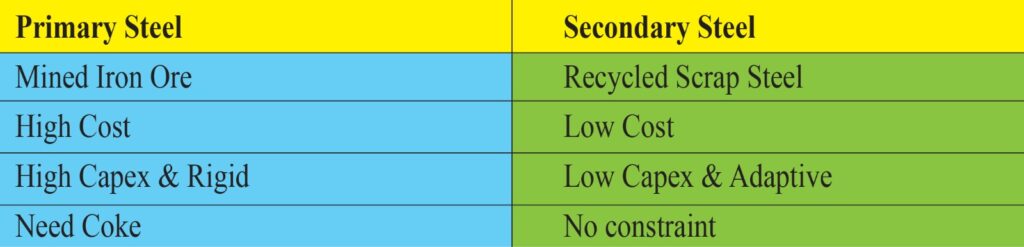
Steel is one of the most competitive sectors. The makers must be efficient and cost-competitive with main producers that create steel from iron ore. To manufacture molten steel, the secondary steelmaking process must employ electric arc or induction furnaces. In India, approximately 45% of steel is manufactured utilising induction furnaces with two major raw materials – Sponge iron and Scrap steel. The primary expense of producing steel is melting, hence the cost efficiency of the SMS becomes critical.
Heart Of An Efficient Sms Process
- High Power Density
- High Melt Rate
- High Yield l Low Heat time
- Low Power Consumption Per Ton
- Less Pollution
- Longer Life of Equipmen
SMS that uses scrap as their primary raw material face significant challenges since scrap is never constant and processing.
Steel Technology
Scrap can be treated using three basic methods: shearing, baling, and shredding. The process identification is determined by the kind of raw steel scrap, its density, size, cleanliness level, furnace size, furnace power density, and other factors. There are numerous types and sizes of equipment available to process scrap from 1 to 100 tonnes per hour.
The majority of the cost of producing steel is power. Dev Energy has been actively focusing on power reduction, including its dynamics and its relationship to scrap processing. The time required for melting is determined by the scrap’s form, density, and size. Improper input scrap leads to longer melting times and increased power usage.
The aim is to process the scrap in the right settings with technology that matches the type of scrap.
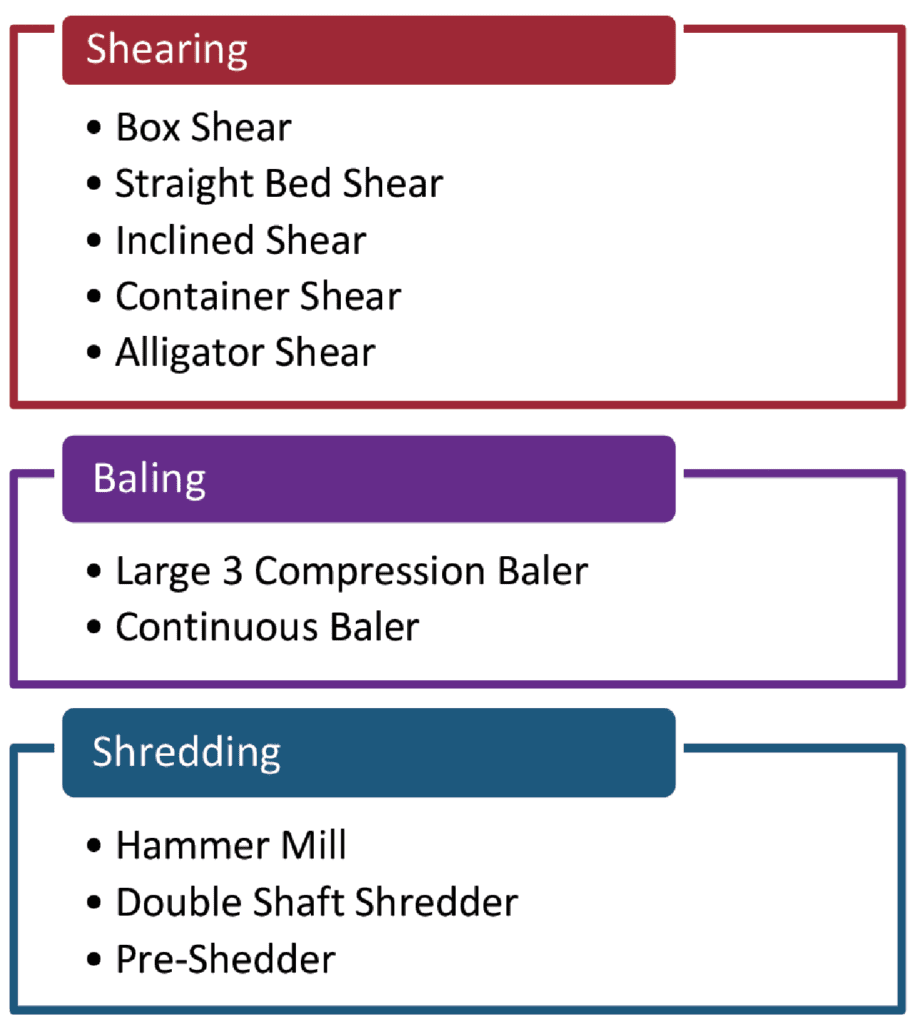
Shredder- Hammer Mill
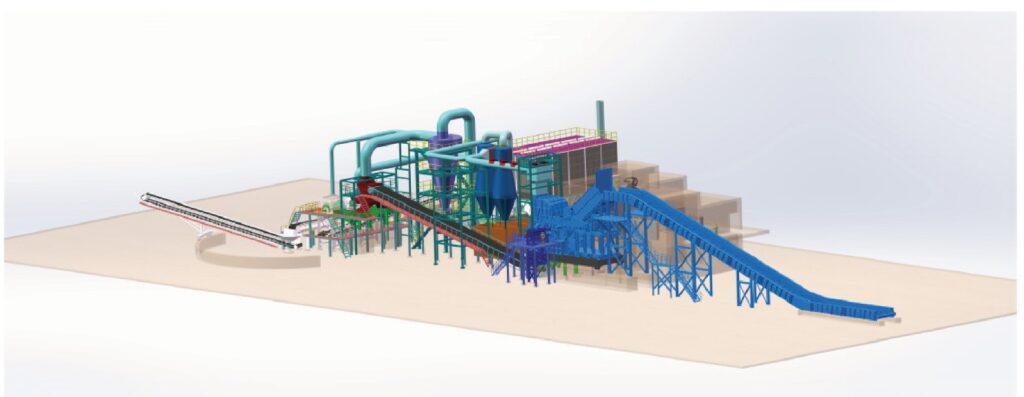
The Hammer Mill Shredders have output density of almost 1.4 ton/m3 with metal recovery of up to 98%. The operation cost of ~ INR 700 /t makes it savings super star for steel scrap melters.
Steel Technology
Innovative solutions in fumes extraction system from the house of Dev Energy results in high dust removal efficiency and clean gas dust concentration is achieved with minimum work zone emissions.
DEV ENERGY developed and deployed a Dog House based fumes extraction system for induction furnaces, collecting more than 95% of the fumes and total power usage is ~10kwh/t.
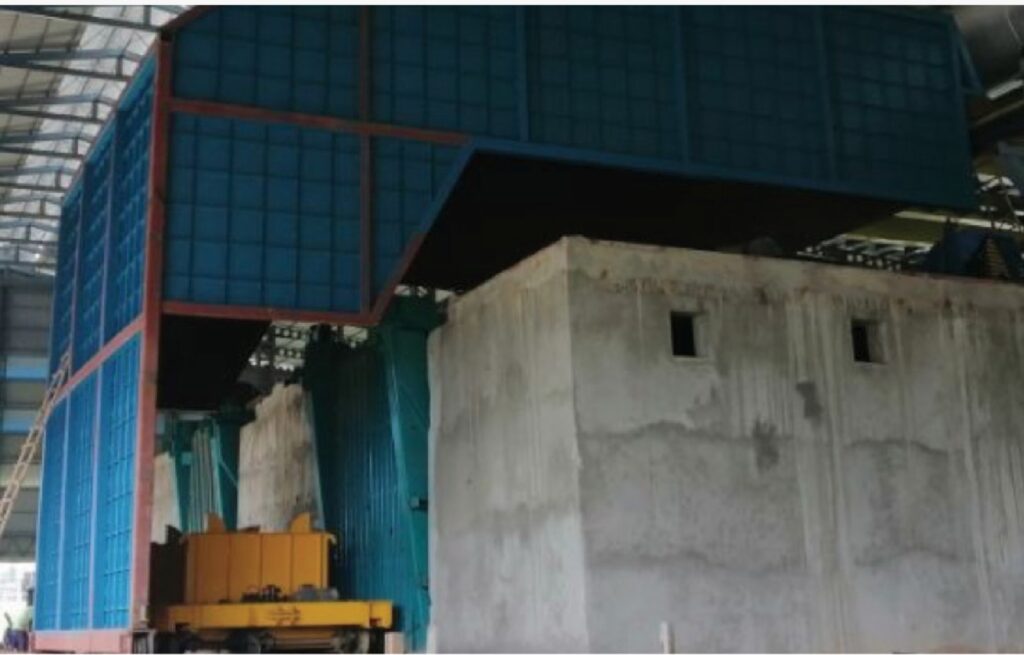
Scrap steel has a large amount of galvanised and painted material that is high in zinc, and the dust recovered typically contains up to ~ 40% of this zinc. This dust can be sold on the market. This converts the DEV ENERGY provided pollution control system into a revenue-generating system rather than an expenditure.
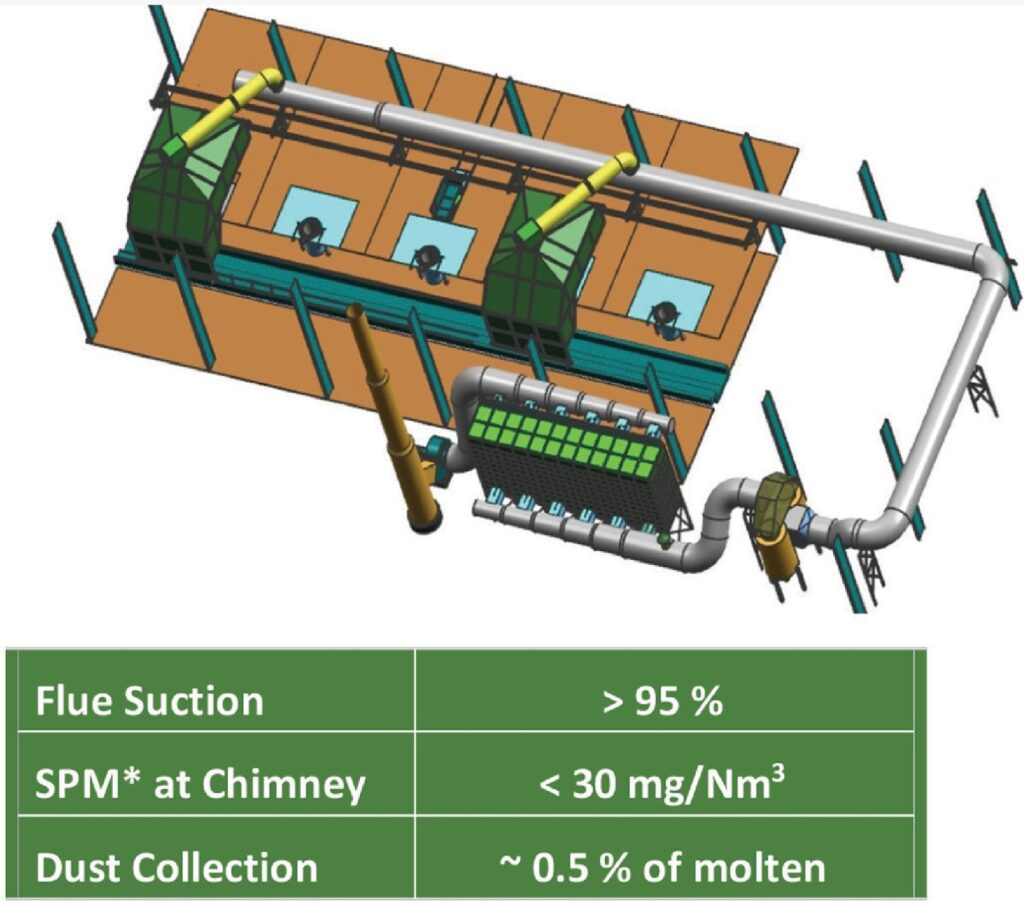
The key performance parameter in compliance of PCB Norms is for the Dog House to suck > 95% fumes and the Bag House f iltration to remove the SPM and exhaust through chimney only under norms.
Scrap Pusher compliments the Dog House system to help SMS furnaces achieve the required melting rate. It has hydraulic operation and rotation on Slew bearing. The telescopic boom on hydraulic motor makes it first choice for users.
parameters cannot be defined, therefore the technologies need to adapt to this variable environment.
The entire process, from scrap purchasing to melting, must be linked with the desired outcome.
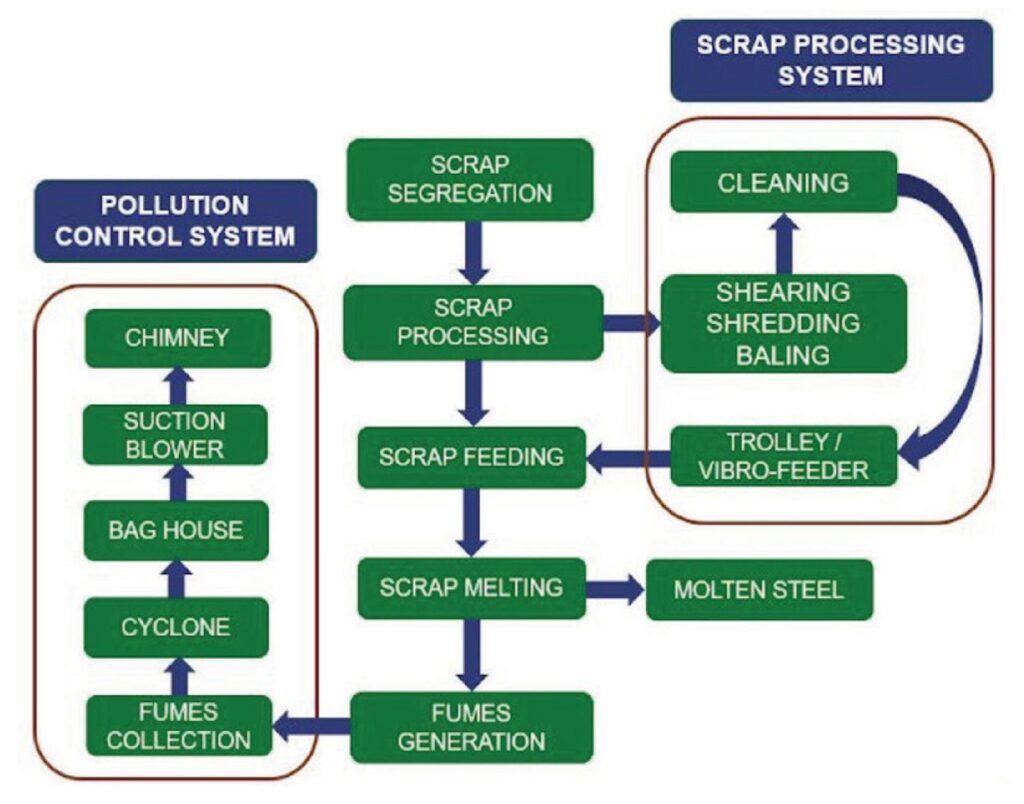
Dev Energy has acquired competence in providing unique turnkey solutions for effective scrap separation, processing, and feeding into the furnace. This feeding system must also be connected with the pollution or flue control system used during the melting process.
Scrap Processing
The scrap processing machines must be selected with reference to the type of scrap that the SMS can source. The machines must be complemented by appropriate scrap unloading and segregation systems. After the scrap is treated, the melt shop design and equipment should be able to feed it into the furnace. Dev Energy offers a full variety of turnkey solutions for scrap unloading, segregation, scrap processing and scrap handling and feeding.
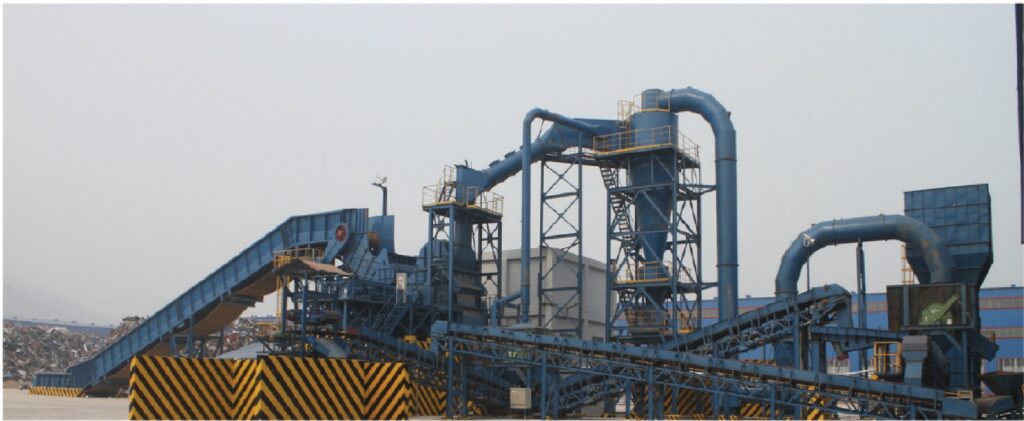
Box Shear
Box shears are ideal for processing a huge variety of scraps. The machine can take all the input scrap and convert it into output of density ~ 1 ton/m3.
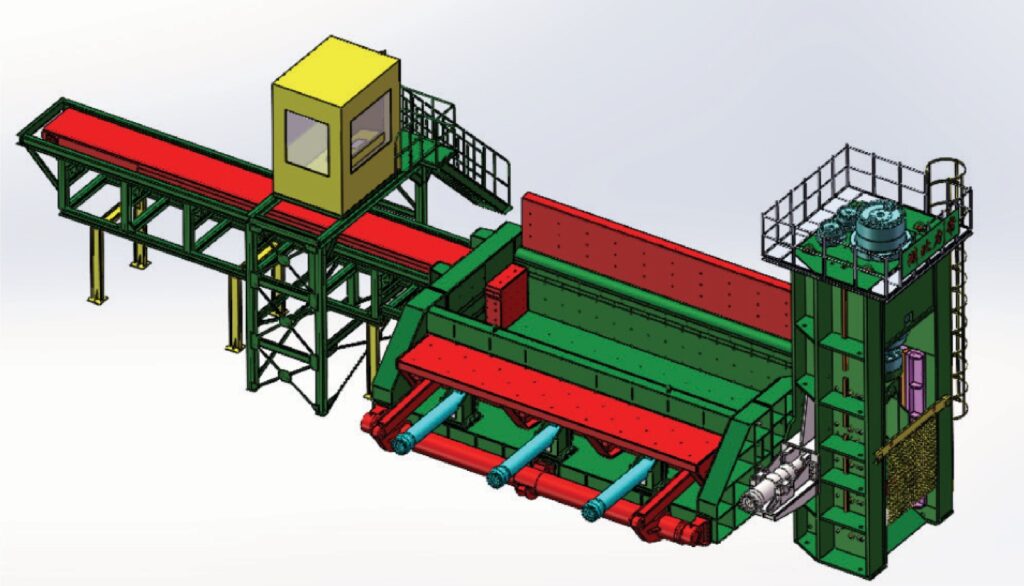
The operational cost of ~ INR 250/t makes it the wisest choices for users.
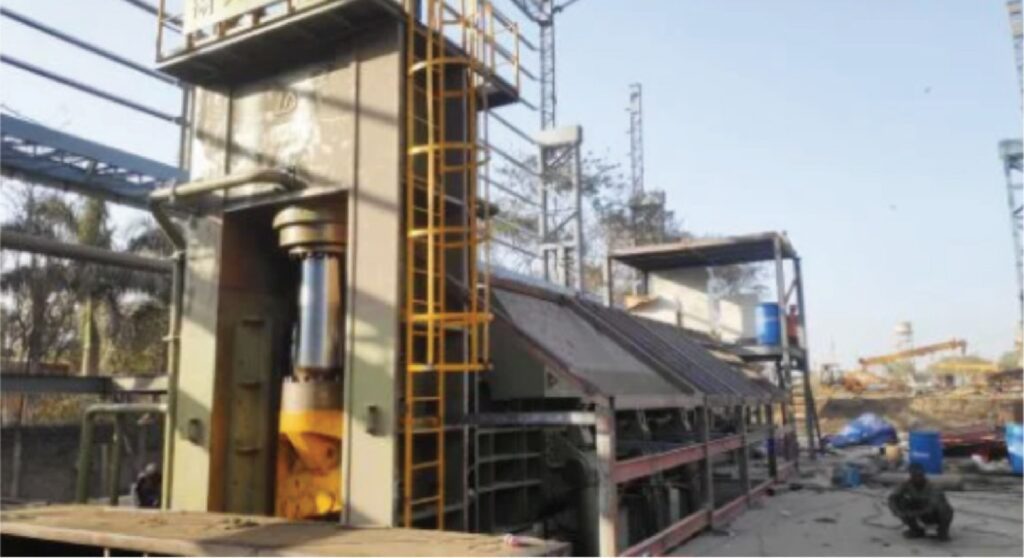
The perfect implementation of superior shredders and shears reduces the power consumption by up to ~ 8% and heat time by up to ~ 10% resulting in overall ~ 10% net cost savings.
Fumes Extraction System (FES)
The National Green Tribunal (NGT) rules and the more stringent Pollution Control Boards (PCBs) have compelled SMS retailers to investigate and reassess flue control system technology. The present devices can only absorb up to ~ 60% of emissions and cannot fulfil government standards. Because they are intended for exceptionally high working pressure, their operating costs are quite expensive.
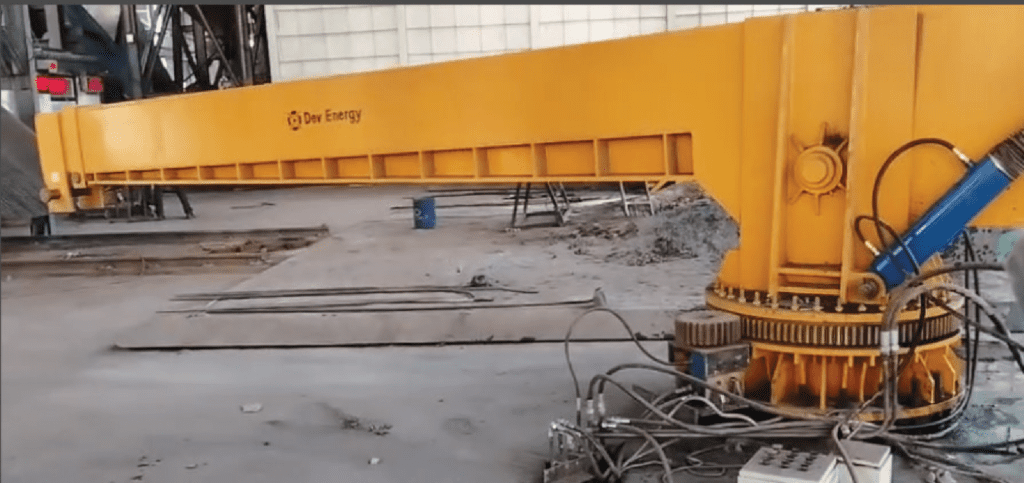
Scrap Charging Trolley which is remote controlled and runs at speed of ~ 30 MPM with VFD DRIVE helps feed the scrap to furnaces without the need for Dog House to be moved. Both back-front and side-travel option are available for versatile layout design.
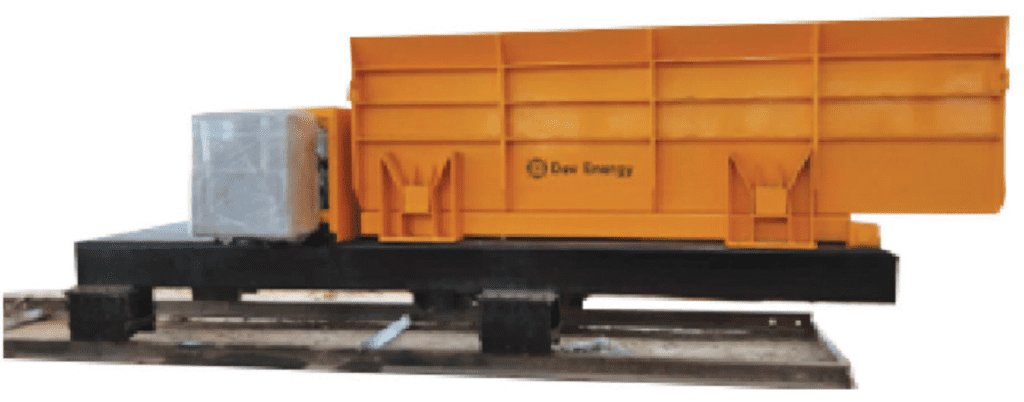
By achieving desired parameters at the outlet of fumes extraction system the workers can do work more efficiently. Higher Yeilds becomes possible once the above mentioned systems are installed and utilised regularly.
Conclusion
Dev Energy is a prominent and reliable provider of end-to-end operational cost reduction solutions for secondary steel melting plants, including scrap processing, scrap feeding and fume extraction systems. With a proven solution offering spanning more than two decades, we have lowered our clients’ production costs while increasing compliance with PCB standards in tighter emission specification limits. Overall, we are devoted to continuing to increase production efficiency in the secondary steel melting shops business.
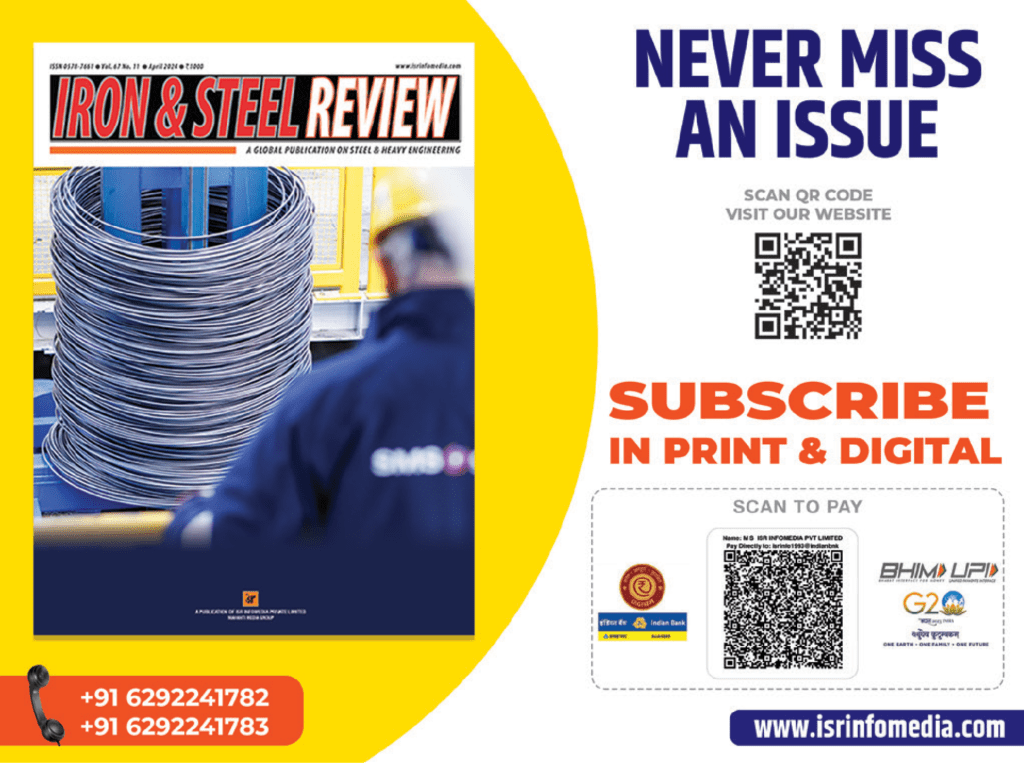